Tackle your supply chain management issues by following our top 3 tips.
The global pandemic may be a once-in-a-generation phenomenon, but the supply-chain issues it has triggered are not. From the rare-earth magnet bubble to the shortage of linear bearings and passive electrical components that hit just two or three years ago, supply chain disruption is a regular event. It can be caused by natural disasters such as the floods in Thailand. It can be triggered by trade wars. Whatever the cause, a supply-chain disruption can cut productivity faster than a power outage. Having a strategy in place to ensure a robust supply chain is essential.
At Motion Solutions, we depend on our supply chain just as our customers rely on us. Over decades as an engineered solutions provider and distributor, we’ve established a robust plan to ensure that our network of global and local suppliers will be there to serve the business so that we can continue to serve our customers without interruption. Here are a few Supply Chain Management tips you can apply to help prevent the adverse effects of supply-chain disruption.
Tip 1: Look for Alternative Suppliers
This sounds obvious but let me unpack it a little. First, this is situationally dependent. If the issue lies with a single vendor or even a single facility (such as when the Tōhoku earthquake shut down the Renesas microprocessor fab for months), finding an alternative source will be easier than in our current climate of broad shortages. In the latter case, if one manufacturer is having an issue, it probably means that the whole industry is facing challenges, which implies a low probability of success. Don’t prepare to deal with trouble when you already have a problem. It’s essential to lay the groundwork for your multisource supply chain well in advance.
Do your homework. Start by identifying multiple suppliers who can meet your needs. Make sure that they have solid disaster preparedness plans in place. Don’t wait to start sending orders to your alternative supplier until after disaster has struck. Instead, throw at least some business their way so that you are an established customer (and closer to the front of the line) when you really need them.
At Motion Solutions, we’ve built up a robust supply chain that combines international partners with local companies. Our team has deep connections with many suppliers, so we’re well-equipped to find options. As a result, we are best positioned to support our customers even during a variety of disruptions.
Tip 2: Go with COTS Designs When Possible
It’s easier to find alternative suppliers when you’re just buying standardized parts. They might still need to be qualified but not need to undergo extensive testing. Use customized parts when they increase the value proposition of your products, but otherwise, design for practicality using commercial off-the-shelf (COTS) components where possible.
If you’re facing a supply interruption with a nonstandard part, then look for a supplier to help design and build alternatives. Because Motion Solutions manufacturers precision stages, we have an extensive inventory of parts (screw stock, end blocks, nuts, etc.). With the help of our engineered solutions team, expert technicians, and dedicated machine shop, we can probably quickly draw up a functionally equivalent design that will act as a drop-in replacement.
Tip 3: Be Proactive
When it comes to tight supply, extra time is like gold dust. We always tell our customers to reach out in advance any time they think they will have issues. If you plan when times are good, it will help us be prepared to work with you when we run into hard times, like right now.
Supply-chain disruptions are a fact of life. Our team has had great success by following these tips to achieve a more resilient supply chain, and you can too. Let us partner with you to succeed even during these challenging times. We offer the resources, experience, and expertise to help you thrive.
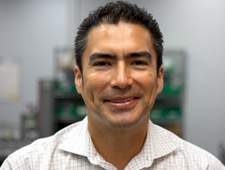
About the Author
Bill Saunders is Vice President at Motion Solutions.
Contact:
Motion Solutions
27 Argonaut
Aliso Viejo, CA 92656
(949) 586-7442
Connect with us on LinkedIn.