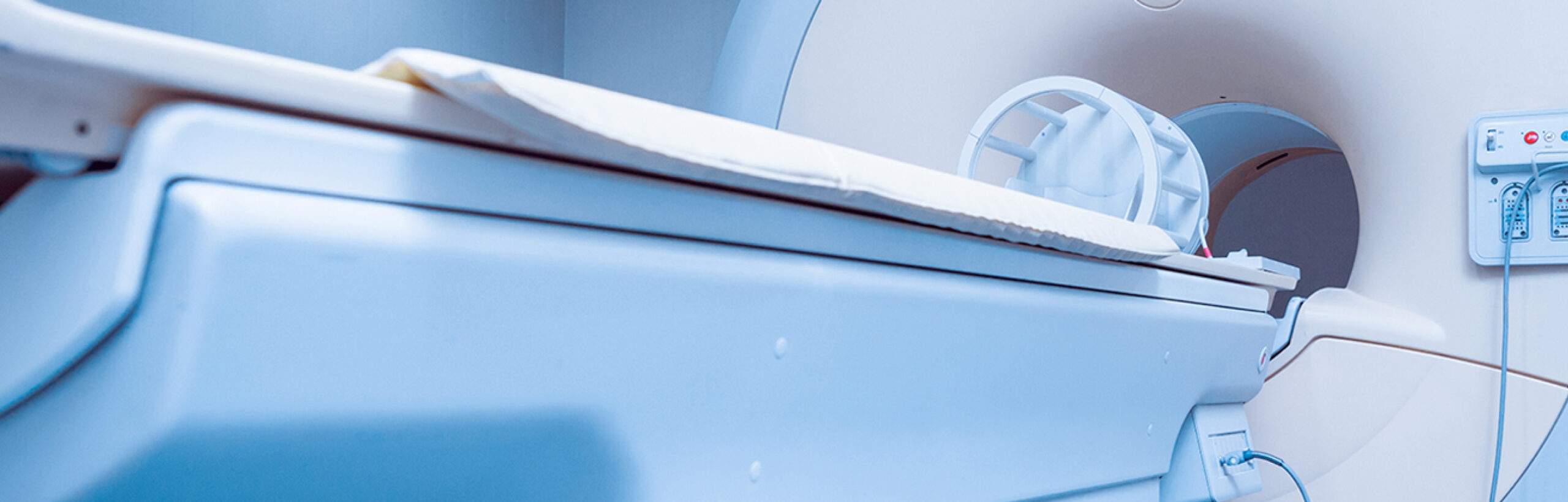
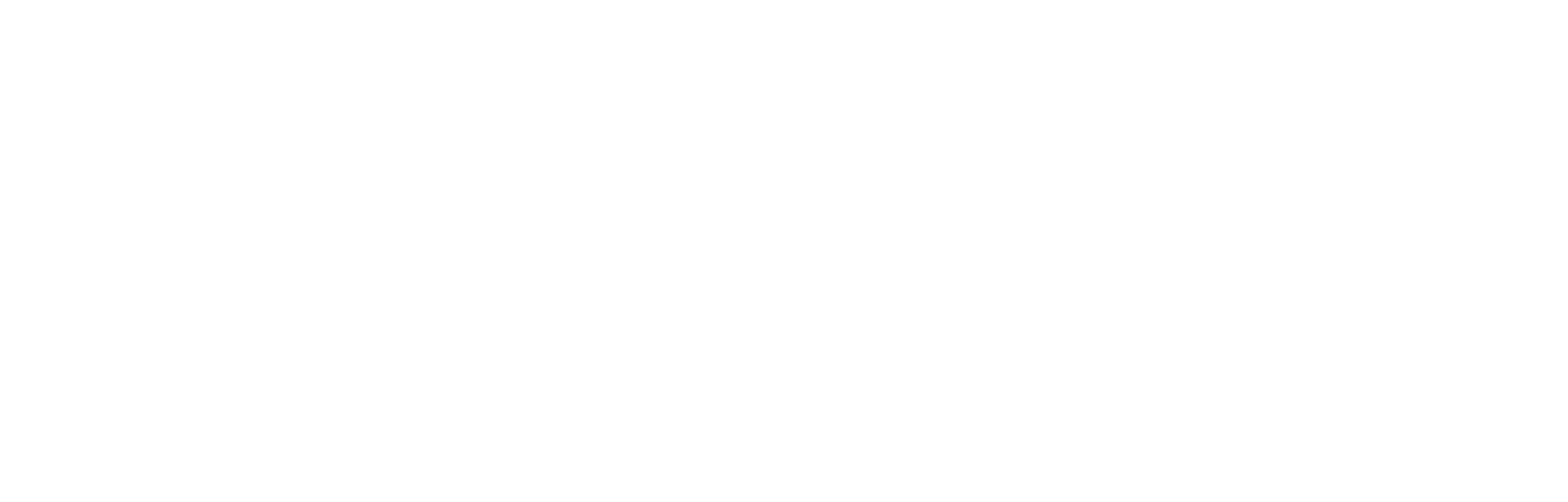
Medical Equipment
Medical therapeutics and diagnostics is a hotbed of innovation.
Here, companies with proprietary core technology tap the expertise of our Motion Solutions team to engineer medical devices and robotic equipment that can improve patient outcomes and save lives. We work with organizations at a variety of levels, depending upon their needs. In some cases, we collaborate closely, meeting on a weekly basis to share design advances, test results, and prototypes. In others, we may re-engineer an existing product to boost manufacturability or decrease costs. Our focus with our medical device engineering is always on addressing client needs, providing the services and expertise that will help them most quickly achieve their goals.
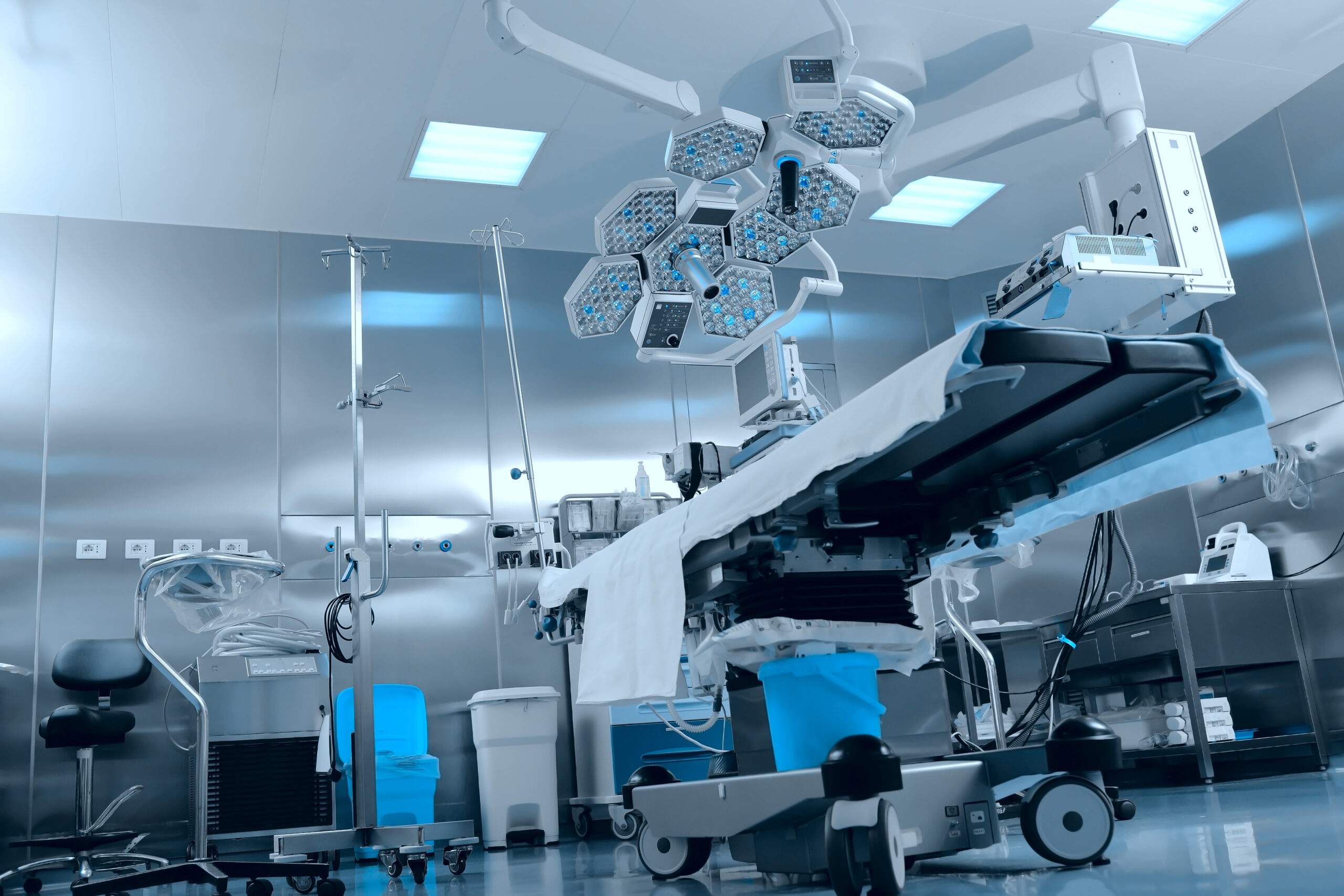
Industry Challenge
The medical sector presents many challenges to manufacturers. Medical devices are engineered to perform to high levels, offering repeatable, reliable performance. Duty cycles may be low but end-users typically expect long lifetimes with minimal maintenance. Devices must meet strict standards for safety and for the generation of electronic noise. If they are patient facing, audible noise may also be an issue. Add to this constant cost pressure and it is clear that medical device manufacturers have their work cut out for them. The role of Motion Solutions is to help them field the best possible product and do it at the lowest price point.
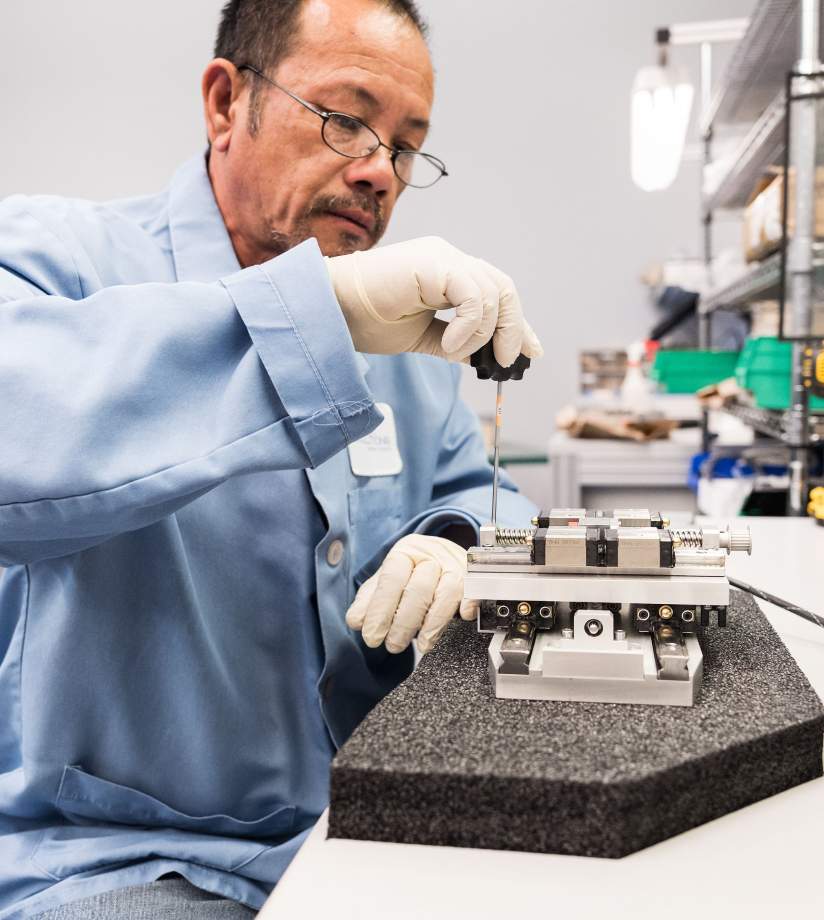
The Motion Solutions Advantage
Motion Solutions has decades of experience in the development of motion systems for medical devices through the design, prototype, and build stages. We understand that patient safety is paramount. As a result, our team has well-defined processes for risk analysis, safety analysis, and failure-mode-effects analysis (FMEA).
Over the years, we have worked on hundreds of devices and systems. Although we approach each new project as unique, we are also able to apply the tools and techniques developed for previous efforts. A detailed five-step process guides our medical device engineering projects, from design, to prototype, to final build. This provides a clear framework for gathering customer input and delivering on expectations. We apply integrated design principles to ensure that our electrical, mechanical, and software teams reach a solution as efficiently as possible.
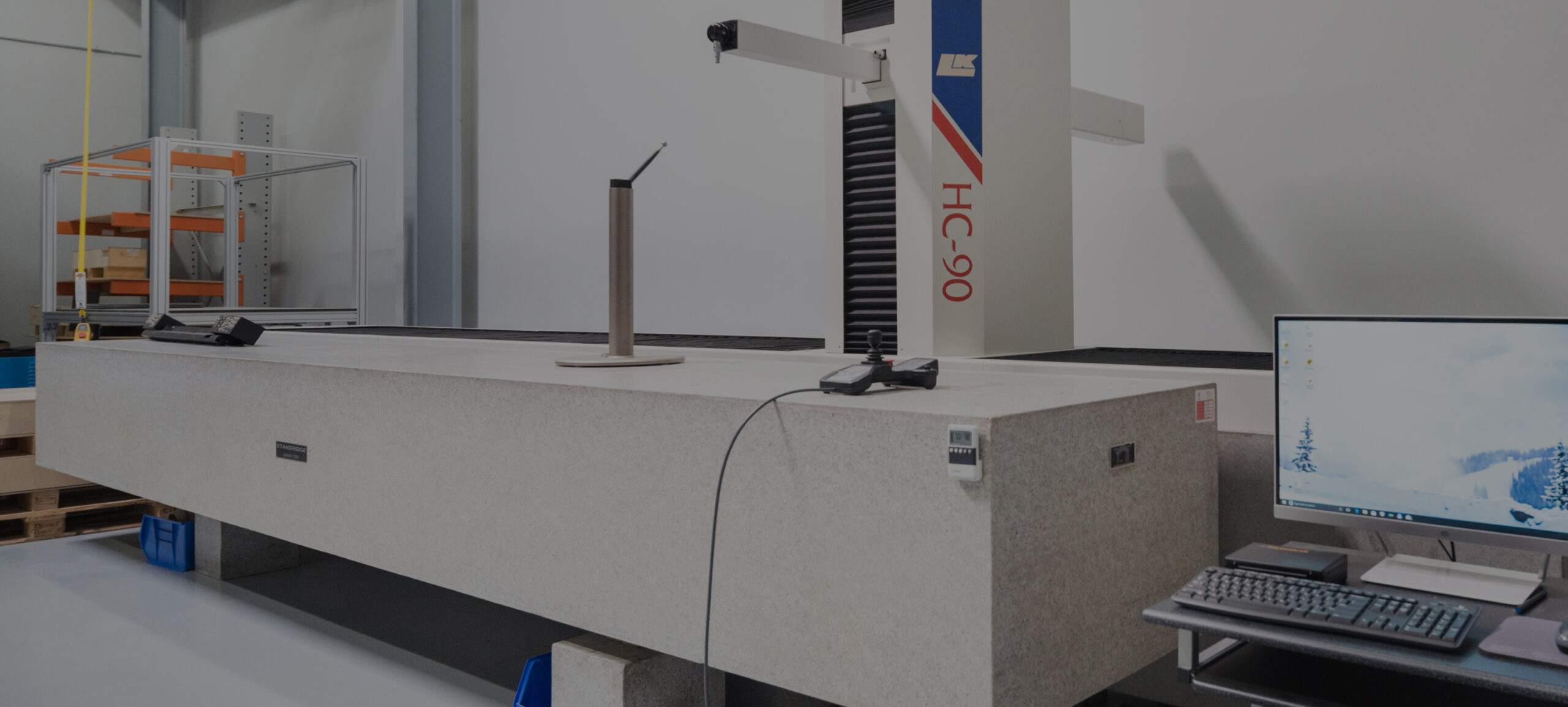
Proven Solutions
Microtomes, precision devices for thin sectioning tissue samples, play a crucial role in biopsies. They produce 5 µm to 30 µm thick slices of tissues ranging from skin to cartilage to bone. Over the past 15 years, our medical device engineering and robotics experts have built an array of microtomes. One of the things we’ve discovered is that the devices need to be extremely rigid in order to avoid introducing ridges or waves in the tissue sample that might create image artifacts. By starting with linear guides based on crossed-roller bearings and optimizing the structure for maximum stiffness, we have developed a baseline microtome design. This starting point makes the process both faster and less expensive for the customer.
The design of automated patient beds helps showcase our safety skills when engineering medical devices. A typical multi-axis patient bed includes many places where the hands or feet of a patient or caregiver could potentially get trapped and injured. We mitigate these risks with redundant safety measures. The system monitors the drive current to disengage in the event of a spike. We also include mechanical limits whereby if the drive forces get too high, the motion assembly will automatically disengage. At this point, the design features both electrical and mechanical safety measures. Good bed design also includes redundant feedback devices on all axes and dual-button control systems to prevent unintended motion.