The Industrial Internet of Things may not reach broad deployment tomorrow but it’s coming, and savvy companies are already making the transition.
The Industrial Internet of Things (IIoT) is inescapable, in more ways than one.Headline after headline trumpets that the IIoT is transforming industry. That plays well in the investor and consumer community. In the engineering world, we’re a little more conservative. Yes, the connected industrial environment clearly has potential to profoundly impact the way industrial businesses work. That holds for everything from engineering to strategic planning to day-to-day manufacturing operations. Will the industrywide transformation happen next month or next year? Probably not. Should you be crafting your IIoT strategy as though it were? Absolutely, and here’s why.
At its heart, the IIoT is about the power of connectivity. Manually reading out temperature or vibration data from a single motor is of limited value. Being able to access health data on all the motors in the entire plant is enormously powerful. Instead of careening from fault to fault, the engineering staff can move into a predictive maintenance regime. They can confidently run their equipment longer without the risk of unplanned downtime, getting maximum performance from the assets.
Multi-location connectivity supports integrated operations management. Here, too, the value is in the volume of the data and its accessibility. If a line goes down at one plant, production across the entire organization easily can be rebalanced, with feeder plants slowing down and other facilities ramping up production to make up for the shortfall. Management can monitor and control assets from across the plant or across the globe using mobile devices.
In these times of lean manufacturing, every manufacturer is looking for new ways to save. The interconnected factory of the IIoT makes it possible to monitor the status and power consumption of all devices, creating the fully visible factory. Add energy analytics to wrangle the data, and the system can identify opportunities for savings. Examples include identifying equipment that is operating (and consuming power) when it should be turned off, to managing peak energy demand in order to get the most favorable pricing from the power company.
Are these examples hypothetical? No, they are real, executed with currently available technology that costs less than you would think.
Getting real with the IIoT
It can be tempting to dismiss the IIoT as hype, but the company that does so runs the risk of being left behind. More to the point, they run the risk of missing out on key benefits, not to mention first-mover advantage. For those organizations interested in exploring the technology, there are a few key techniques for success:
- Do your homework: Find out what the technology can do and how it applies to your particular operations.
- Have a plan: Don’t just slap sensors on every device that moves and start harvesting data. Plan your project with the same amount of effort you would apply to engineering a new product.
- Start small: Identify pain points and conduct a restricted pilot program. The lessons you learn with this initial effort will pay off down the road.
- Play the long game: Although you may begin harvesting data immediately, it takes time to get to know your assets and begin accruing value. Be patient
At Motion Solutions, many of our partners provide products used to create the visible factory. Examples range from sensors to smart drives to components designed to port data from the shop floor to the top floor. Reach out to us to discover how we can help support your IIoT strategy.
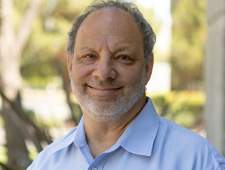
About the Author
Peter Hoffman is vice president of marketing, Motion Solutions.