The term “closed-loop” in nanopositioning indicates that a sensor is used to monitor the position of the stage in real-time. These readings feed back to the controller to provide error correction for the system. Closed-loop control ensures that the nanopositioner reaches the desired commanded position. nPoint uses interferometric calibration for each stage to confirm position throughout a movement or scan. Digital electronics allow for calibration features that are not available in simplistic analog control. This ensures the accuracy of scans not available with other non-calibrated systems on the market. Closed-loop control provides fast, accurate positioning with minimal piezo drift.
Closed-loop also allows for faster control movements such as in step and settle applications. The following is an example of a long travel nPFocus400 stage with a 220g microscope objective. Data is taken directly from nPControl GUI, standard with every controller. PID control and notch filters are used to achieve the settling time in closed-loop. More information on setting these parameters are available on the nPControl Software Page.
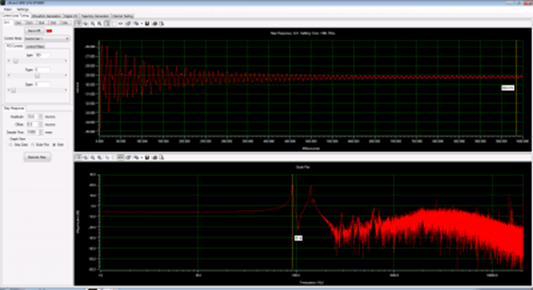
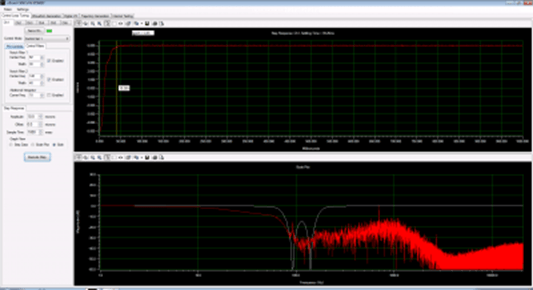
Linearity deviation is the error between the actual position and the first order best fit line. Linearity deviation in open-loop will typically be 7% while the deviation of a calibrated system using capacitive sensors will be lower than 0.01%. As an example, on a 100µm stage the actual position of the stage can have a deviation up to 7% over the commanded position at any given location within the scan. This could result in a location deviation of 7µm. A commanded position of 50µm could be within 43µm and 57µm. A similar closed-loop system with a linearity deviation of 0.01% would be within 50.01um and 49.99um for a commanded position of 50µm.
Closed-loop control also reduces drift effects of the piezo actuator. During the first minute from when a signal is sent to the actuator drift will be approximately 0.5% of the travel range. The second minute of operation will have approximately 0.1% drift. After this time, the percentage of drift will steadily decrease to less than 0.02% per minute. When used in closed-loop control, piezo drift is dramatically reduced to maintain position as long as the system is under power.
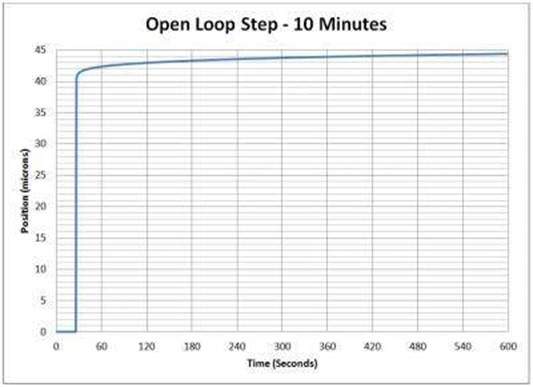
open-loop drift over a 10 minute period.
Open-loop systems have lower noise (and resolution) than a closed-loop system because the sensor noise and driver compensation is eliminated from the system. nPoint’s piezo stages are listed for resolution in closed-loop. Electronics’ resolution and noise will often be the limiting factors in open-loop resolution. nPoint electronics have 20-bit resolution.
Closed-loop control is important for most positioning applications. Certain applications allow a user to close their own loop with external feedback methods (interferometric etc.) that can interface directly to nPoint controllers. Open-loop control is an economical choice for applications where known position with internal sensors is not necessary or where step and settle speed is not as important.