Editor’s note: In this ongoing video series, members of the Motion Solutions engineering staff share insights on technologies and problem-solving. The Motion Solutions Engineered Solutions team works daily to design complex electromechanical assemblies across a variety of industries. With more than 300 years of aggregate design experience, they have deep expertise in designing customized bearings for a range of demanding applications.
Cleanrooms play an essential role in contamination-sensitive applications such as semiconductor fabrication, pharmaceuticals, optics, medical devices/life sciences, and many more. Cleanrooms are designed to control the number of particulates in the air, such as dust, microbes, aerosols, etc. to avoid compromising the processes and products manufactured within. The standards for these enclosures are extremely tight, especially when motion systems are involved, but by following a few basic techniques, it’s possible to conduct operations while maintaining an appropriate environment.
Cleanrooms are classed according to standards that specify the number of particles of a specific size per unit volume of space (see table).
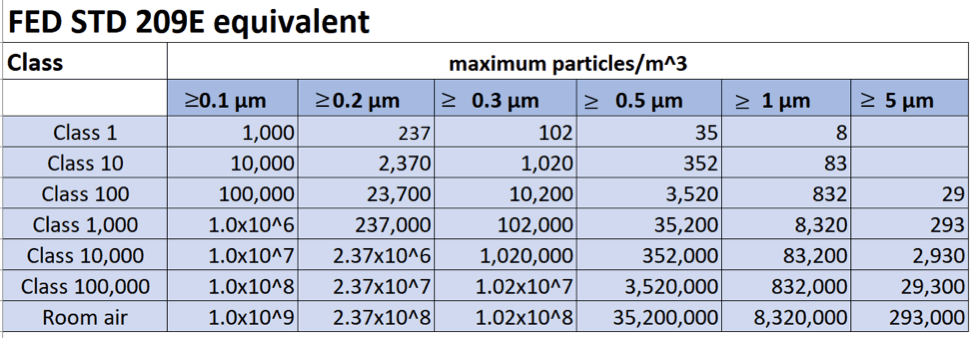
Particulate control is achieved by a dual strategy of filtering the air of particles and minimizing introduction of new particulates from personnel, materials, and equipment.
Controlling particulate generation can be a challenge, particularly when the cleanroom encloses machinery. Micro-lithography, for example, makes heavy use of robotics and other motion systems. Moving equipment such as linear guides, if improperly specified, can generate fresh particles. With proper techniques, however, a linear motion system can support operations in a Class 100 cleanroom as easily as on a factory floor.
Controlling contact
Linear bearings involve multiple instances of surface contact. Ball-style bearings, for example can generate metal fragments from the balls contacting each other. One solution to minimize that contact is to enclose and separate the balls in a ball cage. Ball cages are plastic or polymer structures designed to maintain separation between balls without altering their friction-reducing capabilities (see figure 1).

As long as the balls are separated by the cages, dust generation will be substantially reduced (see figure 2).
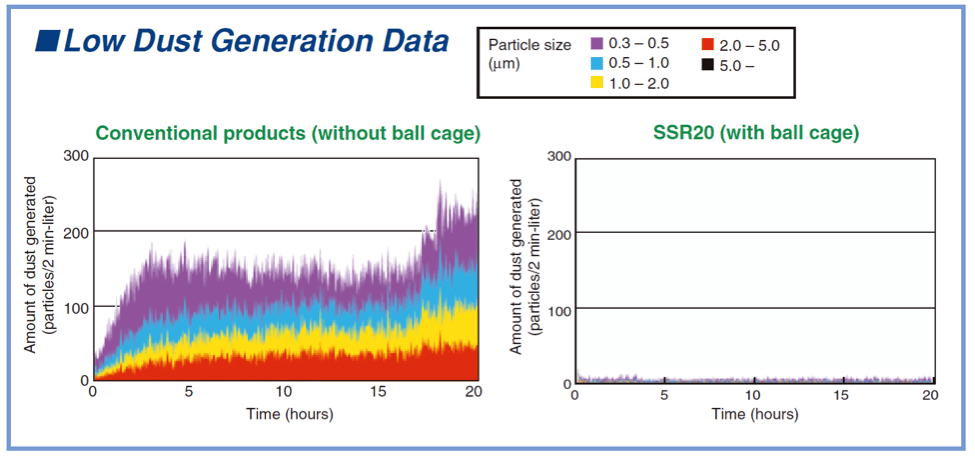
There is a common misconception that ball cages increase price and/or leadtime but that is not generally the case. For the most common models, there is no price difference. Ordering a linear guide with ball cage is a smart way to increase lifetime and improve cleanroom performance.
Preventing corrosion
Corrosion is another source of particulates. Standard-grade carbon steel oxidizes in wet or humid environments to create rust. This is a concern for applications such as semiconductor and laboratory analytics, which involve reagents, or even manufacturing processes that take place in human environments. In these types of cleanroom applications, corrosion control measures should be specified. Options include:
- The use of an appropriate grade of stainless steel
- Applying anticorrosion coatings such as hard chrome or black chrome
Although these measures are effective, they can add significantly to the leadtime of the part. When an order comes in for a bearing with an anticorrosion coating, for example, the manufacturer will not modify a bearing already in stock. Instead, they will build the bearing from scratch, coating each element before assembling the bearing. This typically results in a leadtime of several months.
Motion Solutions offers customers an alternative. We have the in-house capabilities to disassemble a standard bearing, send it out to a local partner for coating, and then reassemble it in-house. Our skilled technicians ensure that the coated bearing meets all performance specifications and tolerances. Because the process takes place locally, leadtime is slashed from multiple months to a few weeks.
Managing lubrication
A final consideration for cleanroom bearings is the choice of lubrication. Although standard organs are designed to reduce rolling resistance, they can spatter and generate particles. Cleanroom greases are specifically formulated for low dusting (see figure 3).
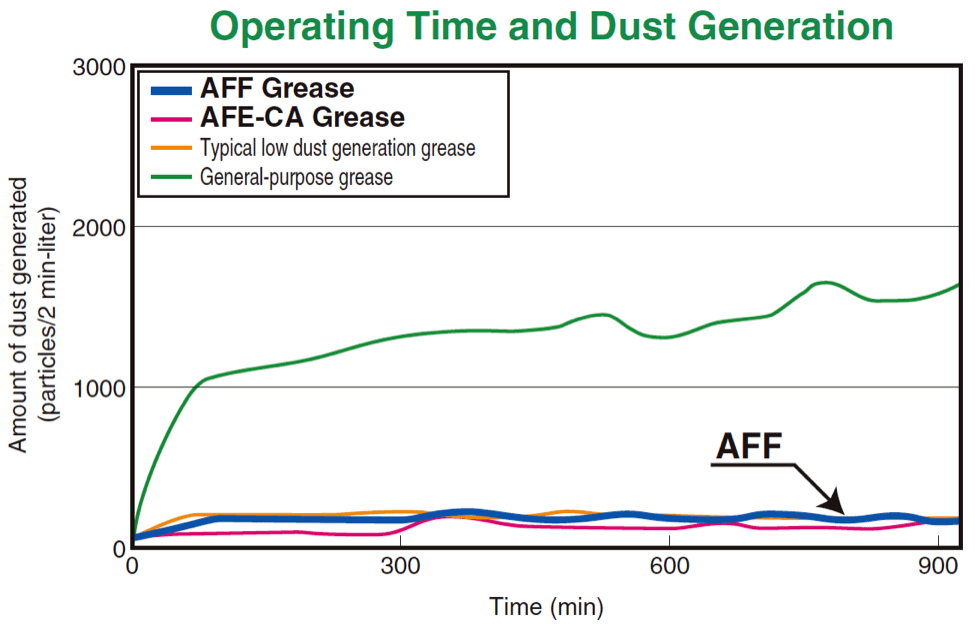
Getting linear bearings packed with cleanroom grease is not as easy as it sounds. Manufacturers don’t simply pull a stock part from inventory and change out the grease. Instead, when the order comes in, they build a linear bearing from scratch and inject the appropriate grease at the end. As a result, ordering these parts can involve a leadtime of several months. From the OEM perspective, buying a stock part and swapping out the grease seems like a reasonable solution, but it can actually be problematic.
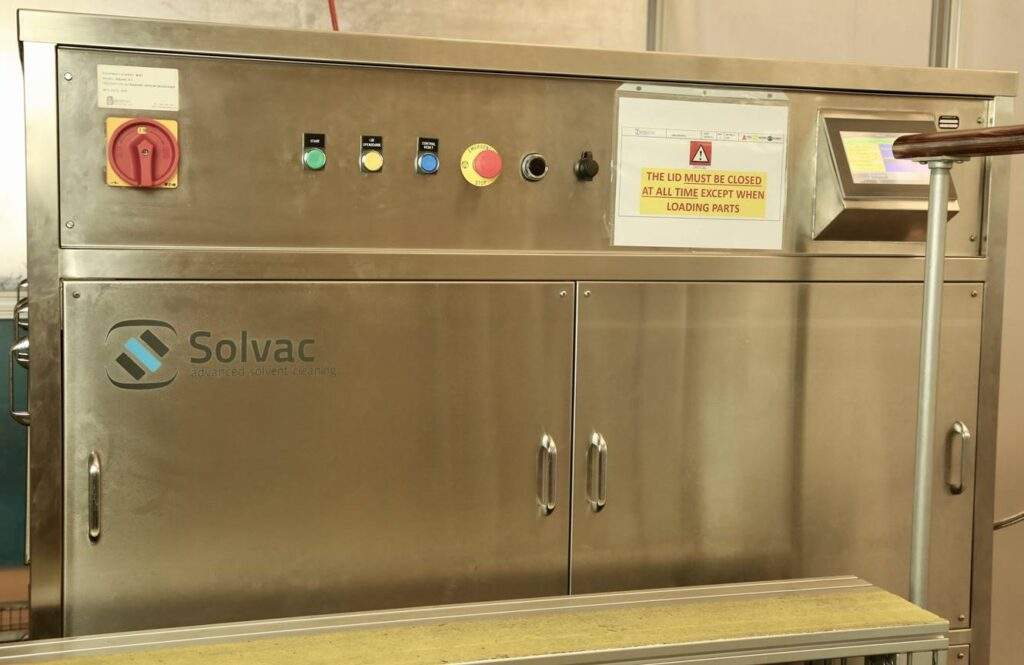
One of the cardinal rules of lubrication is that greases should not be mixed. Doing so can cause lubrication breakdown, part damage, and premature failure. Particularly in caged bearings, it’s very difficult to remove all of the grease before replacing it. This is an area in which Motion Solutions can bring our unique combination of expertise and specialty facilities to bear. At our primary production facility, we have a degreasing tank that enables us to remove all traces of the old grease before replacing it with new (see figure 4). Our skilled technicians are expert at changing out grease while maintaining performance, all in a fraction of the time required for factory orders.
Trust your vendor
Cleanroom applications are typically high-value operations with a high cost of downtime and significant cost of scrap. To protect operations and maximize OEE, take care to properly specify linear bearings to operate in this unique environment. Minimize dust generation by choosing caged bearing guides and specifying corrosion resistant components where appropriate. Be sure to call out cleanroom greases and take advantage of local expertise to minimize leadtime. Most important, work closely with your vendor to ensure that you are making the best choice of components and processes to ensure the success of your application.
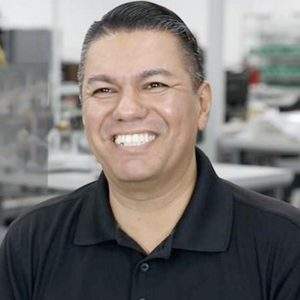
About the Author
Alex Polo is a Sales Engineer and linear motion specialist at Motion Solutions.