Piezo stages are typically used in applications that require fast motion with extremely high resolution and accuracy over ranges that are less than 1 mm. The challenge arises in applications that need nanoscale accuracy but over a range of multiple millimeters, for example, high-resolution microscopy, or semiconductor fabrication. In these types of cases, Piezo stages alone can’t do the job. These applications benefit from hybrid positioners that combine mechanically driven stages with piezo stages. The electromechanical stage provides the extended range of travel while the piezo element performs the final positioning. The result is a hybrid device that can reliably satisfy both sets of requirements.
Piezo stages
A piezoelectric ceramic expands under an applied voltage. Piezoelectric positioners have no moving parts and no friction, so they are highly reliable over billions of cycles. With proper drive electronics and closed-loop feedback, they can deliver sub-nanometer resolution and nanoscale precision with millisecond step-and-settle times.
Mechanical Stages
Engineering teams often use precision electromechanical stages based on linear motors or screw-driven stages to achieve long distances of travel while still maintaining micron-scale accuracy. Equipped with precision linear guides and high-resolution closed-loop feedback, these mechanical stages can deliver great stiffness and in-position stability.
The most significant drawback to screw-driven stages for high-precision applications is limitations to accuracy and resolution. The mechanical nature of the stages prevents them from repeatedly advancing in nanometer-scale steps.
The best of both worlds
Hybrid stages combine piezo actuators with electromechanical positioners to deliver the best of both worlds – a stage that can repeatedly and accurately execute steps of only a few nanometers over ranges of multiple millimeters. The mechanical actuator performs the macro-scale positioning and the piezoelectric actuator completes the move with nanoscale resolution.
Piezo stages and electromechanical positioners can be combined in a variety of ways, each with its own advantages and disadvantages. A common approach is to connect the two actuators in series and use them to move a load mounted on a linear guide (see figure 1).
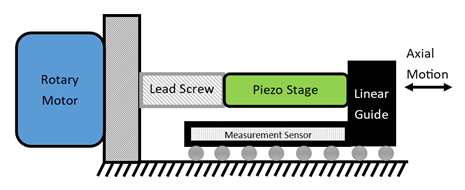
Successfully executing this design requires care. The system requires complex control electronics and high-resolution linear feedback. The end result is a product that offers several millimeters of motion and high holding force combined with single nanometers of resolution and repeatability.
Hybrid stages in action
To demonstrate the concept, we tested a hybrid stage that combines our piezo stage technology, a screw-driven linear actuator, and a precision linear guide. The motion range of this hybrid stage is 50 mm. For feedback, we used a linear encoder with 1-nm resolution.
A screenshot of our GUI shows that we can command the stage to move 1 nm, if needed. We applied no averaging
(see figure 2).
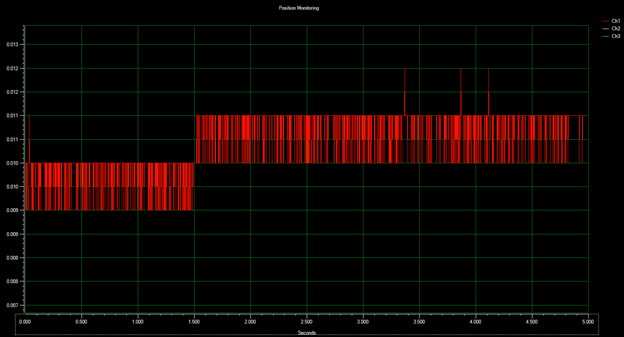
Figure 2: Screenshot of the nPControl GUI that demonstrates a displacement of one encoder count, 1 nm. The vertical scale mark is 0.5 nm.
We test the position repeatability of the stage by commanding it to perform nm-level steps, typically a challenging demand for a screw-driven stage.
In the data presented below, we command the stage to perform twenty consecutive 500 nm steps in one direction followed by the same in the opposite direction. We record the motion with an external interferometer. There are two main points to take away from these data:
- The backlash common on screw-driven stages is now absent since the piezo is correcting the final position.
- The bidirectional repeatability is excellent.
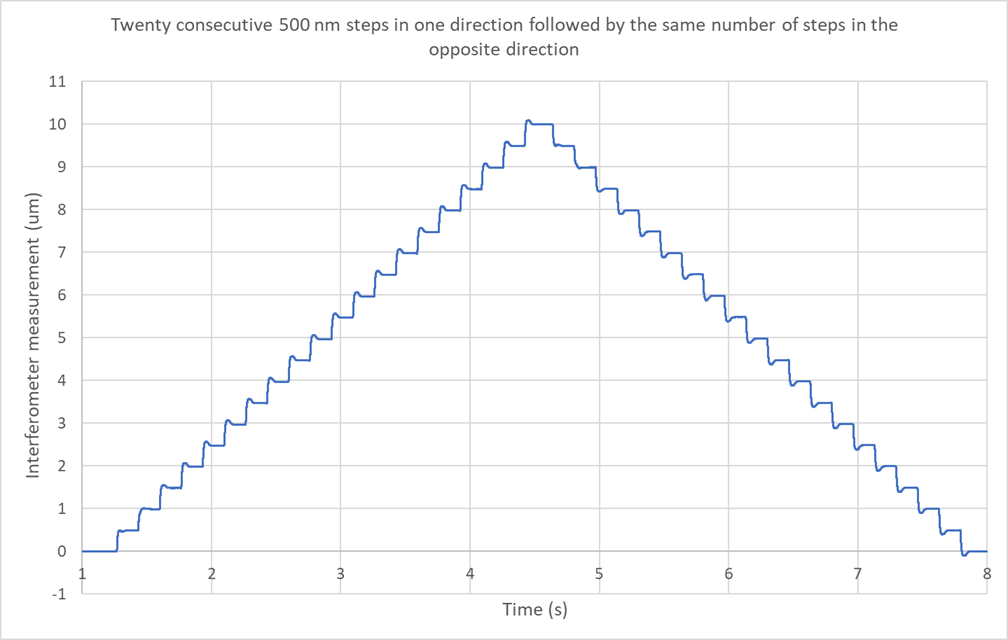
Figure 3: Twenty consecutive 500nm steps in one direction followed by the same number of steps in the opposite direction. The vertical scale mark is 1 um. The data is taken with an interferometer and no averaging is applied.
The hybrid stage can also be commanded to perform piezo-only motion. This may be required when single nm-level repeatability is desired throughout motion ranges that is within the piezo capabilities. In the data presented below, we commanded the stage to perform 100-nm steps. We record the motion using an external interferometer (see figure 4). The vertical scale mark is 100nm.
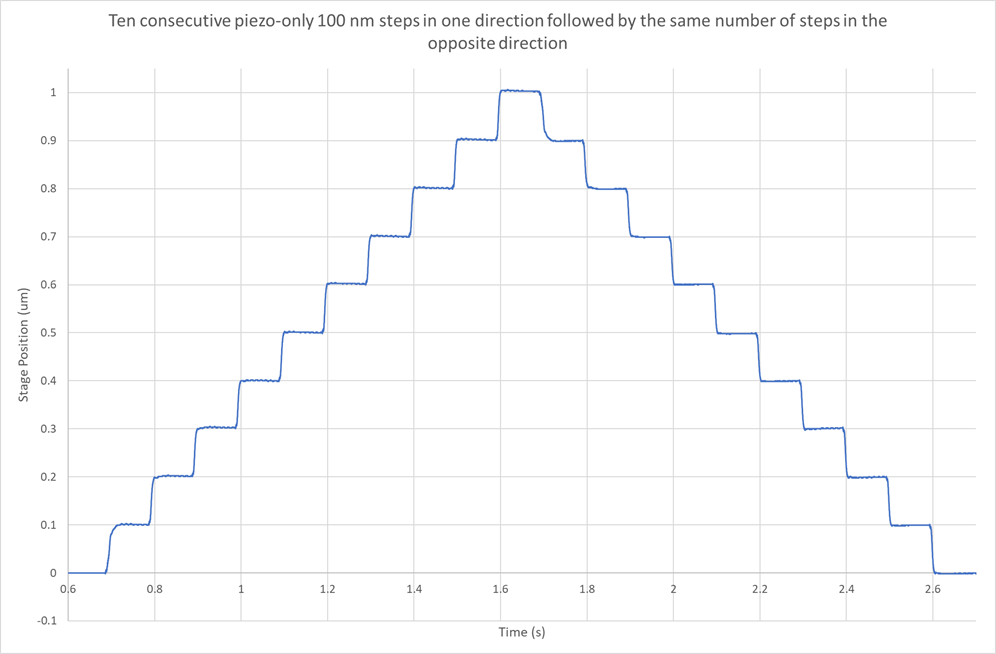
Figure 4: Ten consecutive “piezo-only” 100nm steps in one direction followed by the same number of steps in the opposite direction. The vertical scale mark is 100 nm. The data is taken with an external interferometer and no averaging is applied.
In summary, for applications that need nanoscale accuracy and repeatability over a travel distance of millimeters, hybrid stages provide a good solution. The screw-type actuator performs the positioning, while the piezoelectric component responds to maintain nanoscale accuracy. The result is a robust, fast, accurate device for a variety of applications in the areas of photonics, semiconductor, biotech, and optics.
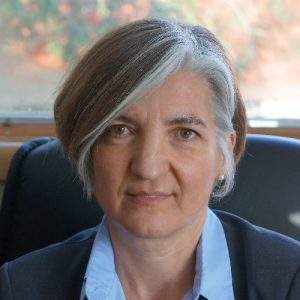
About the Author
Katerina Moloni is the Director of Nano products at Motion Solutions.
Contact:
3030 Laura Ln
Suite 100
Middleton, WI 53562 USA
www.npoint.com
www.motionsolutions.com
Connect with us on LinkedIn.