Postpartum hemorrhaging is a major cause of maternal mortality in the developing world. The condition requires immediate medical treatment and transfusion with appropriate blood products. Accessing a blood supply might be straightforward in an urban hospital but in the rugged rural terrain of countries like Rwanda, surface travel from a blood bank to point-of-care can take hours; meanwhile, lives hang in the balance.
To address the urgent need for postpartum care, the engineers and entrepreneurs of Zipline have built a drone system that can deliver blood products to patients and their doctors in an average of 30 minutes. Developing a system that can perform in the face of tough environmental conditions and uncompromising reliability requirements presented enormous challenges. With the assistance of Motion Solutions, Zipline has met those challenges, deploying systems that routinely make as many as 50 deliveries a day.
Nicknamed the Land of 1000 Hills, Rwanda is a country of harsh topography and a tropical climate marked by heavy rains and high winds. Manned air transport might avoid rough roads and obstacles but it is infrastructure intensive. The aircraft are expensive and have higher cost of ownership than drones. In addition, they require runways and last-mile transportation, while exposing pilots to the risks of rough weather. Drone-based delivery provides a better option.
During operation, a Zipline drone is loaded with blood product at a central distribution center and launched into the air to be directed to its destination by autopilot. Rather than landing, the drones deliver their payloads by parachute. Although manned aircraft can do the same, the smaller, lighter drone aircraft can fly lower, precisely targeting the location of the drop. After the drone releases its payload, the aircraft reverses without landing to return to the distribution center. There, it is captured, refueled, and loaded for another trip. The drones have a 80-km service radius (160 km round-trip). In partnership with the Rwandan government, Zipline currently operates one distribution center that enables instant delivery at a national scale.
Simple and rugged
The Zipline team developed much of its system in-house. This includes the controls platforms, the aircraft, and even the aircraft motors. For the motion components used by the launch and recovery systems, however, they turned to Motion Solutions.
The drones are launched with a system that can accelerate one of the 21-pound aircraft from 0 to 110 km/h in 0.6 s. The drone is mounted on a rail-guided carriage. The carriage is driven by a continuous loop of cable that is itself driven by a motorized spool (see figure 1).
During launch, the cable/motor combination initially applies high acceleration to the carriage, reeling in the cable on the acceleration side while unspooling the cable on the deceleration side. When the drone is 90 percent up the launch rail, the cable/motor slows to deceleration mode to enable a soft release. To further decelerate the carriage, the system includes an eddy current brake.

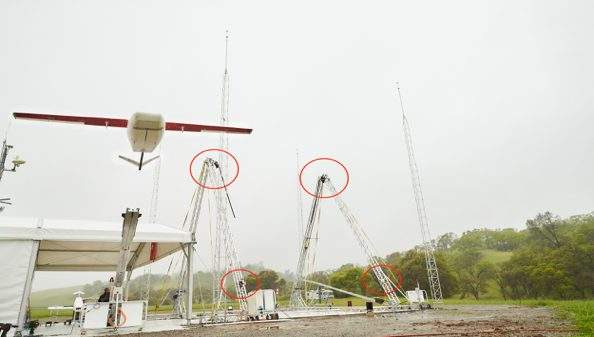
The recovery system needs to not only capture the aircraft but decelerate it safely and without damage. The system consists of two long, parallel carbon fiber tubes that are attached to a truss structure via a gearbox and mounting plate and positioned in elevation by rotary servo motors (see figure 2). Cable runs up through the first carbon fiber tube from its base to its tip, then across free space to the second tube, then down through that tube to an uptake spool at the base. This forms an adjustable horizontal arresting line between the two carbon fiber tubes.
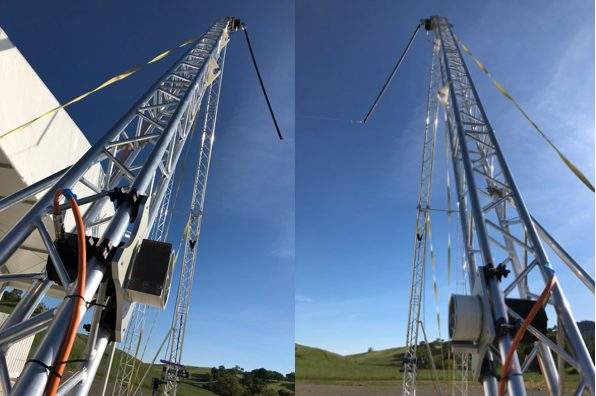
When the drone comes in to land, the motors position the arrestment line to catch the tail hook of the aircraft. An additional rotary servo motor adjusts spool speed to control cable tension so that the drone is decelerated gradually.
Rugged components
If function is important, reliability is absolutely essential. “The lives of people depend on our service, so, ’Sorry, the technology is down,’ is not really an option for us,” says Eric Watson, systems engineer and program manager at Zipline. “Also, we’re operating in the real world. We have neighbors at the distribution center. We’re flying over their houses and streets, so it is important for us to have really high reliability.”
Although Rwanda’s elevation results in reasonably mild temperatures, the weather is marked by rain and high winds. The team needed components that could tolerate moisture and dust, as well as high duty cycles, while remaining affordable. That was where the Motion Solutions team came in. Zipline worked with Motion Solutions to source servo motors, servo drives, gearboxes, and electrical wiring harnesses.
Zipline addressed the issue of reliability using its standard three-prong strategy. First, they designed for high reliability. That process started with engineering simple, robust systems. Once the preliminary design was established, they worked with Motion Solutions to develop high-reliability components capable of surviving 24/7 exposure to the tropical environment of Rwanda. That process involved determining the failure modes of the various devices and developing methods to harden against those failure modes. To produce a ruggedized motor, for example, Zipline operated a unit for six months in the heavy salt fog at its coastal California test center, followed by a six-month deployment in the dust and torrential rain of Rwanda. Motion Solutions and its manufacturer partner analyzed the unit to determine failure modes and developed a strategy for hardening against them.
Motion Solutions was involved from the very first prototype. The process took place in two steps. The first step was to solve the problem from a technical standpoint. The second step was to take the information gleaned from that iteration and develop a version that both solved the problem and did so at a commercially viable price point.
“The Motion Solutions team did a great job of interfacing with the supplier to identify the critical design elements that would give us the most bang for our buck,” says Watson. “I think the three of us—Zipline, Motion Solutions, and the motor manufacturer—worked together really well to come up with a good solution.”
Guarding against systemic failure
The second prong of the reliability strategy was to seek out and protect against systemic failures. This required comprehensive testing during design and deployment, both on a hardware and software level. Here, too, Motion Solutions provided assistance. “Motion Solutions has been really good with helping us diagnose those failures and then modify the design so that we don’t see those failures again, especially around environmental challenges,” says Watson. “That’s something that has been really helpful for us, closing the loop on the failures that we’re seeing in the field.”
The third aspect of high reliability is to design for fast diagnosis and recovery from faults. The company target is to be able to swap out any replaceable unit within five minutes of downtime. “Not only are we selecting high-reliability components, but from the beginning we are designing the system in such a way that we have the ability to do an easy swap on these components if there is a failure in the field,” says Watson. “How do those come together in such a way that the maintenance technicians can quickly of take them apart, put them back together with a replacement part?”
Supporting deployment
In a project of this scope, logistics also play a part. The rollout of the Rwanda distribution centers, for example, was tightly scheduled. When a machine failure at the factory of one of the motor vendors threatened to delay delivery by four months, Motion Solutions reached out to Zipline to find a workaround. “Motion Solutions really stepped up to identify a different motor that was not only more readily available but fit the application better,” says Watson. “To their credit, it wasn’t a case of us asking whether they could find another motor for us. It was really Motion Solutions saying, ‘Give us some specs. Let us dig around and see if we can find a way to solve this problem in the next few days.’ That was a key area where Motion Solutions provided a ton of value to us.”
The Rwanda network is just the start. Zipline has plans over the next year to launch four distribution centers in Tanzania that will serve 10 million people across 1000+ health facilities. Tanzania is at a much lower elevation than Rwanda, so the systems will need to tolerate much higher temperatures. Zipline’s project management team is working closely with Motion Solutions to ensure successful rollouts that scale with Zipline’s needs.
Another aspect of Zipline’s future development is exploring ways to boost the number of deliveries that each aircraft and distribution center can make per day. “We expect those improvements to include automating some processes that are manual today,” says Watson. “Motion Solutions’ experience with automation and machine design—their engineering support as well as component selection and vendor relationships—will go a long way in helping us take on some of these new projects.”
As to the work done on the Rwanda project, the Zipline team seems more than satisfied with the results of their collaboration with Motion Solutions. “I’m really happy with the system that we have,” says Watson. “We have been able to come up with a cost-effective solution that is also really going to improve the reliability.”
This start-up beat Amazon, UPS and FedEx to the punch with drone deliveries from CNBC.
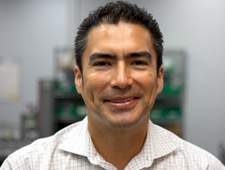
About the Author
Bill Saunders is the Vice President of Sales, Motion Solutions.