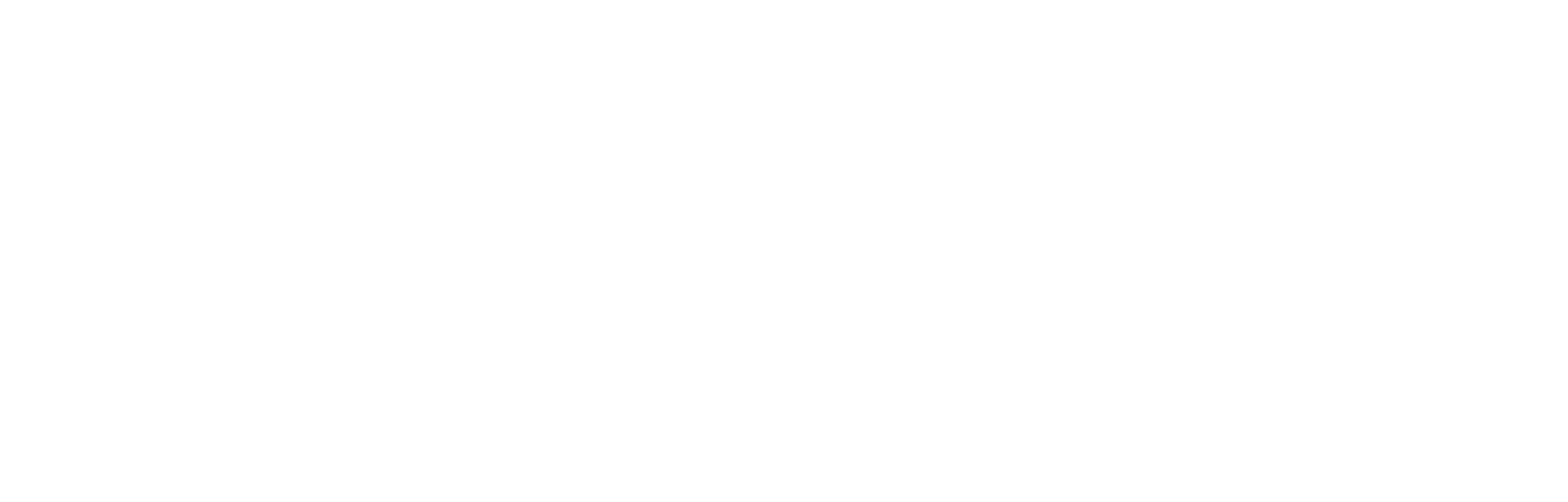
White Papers
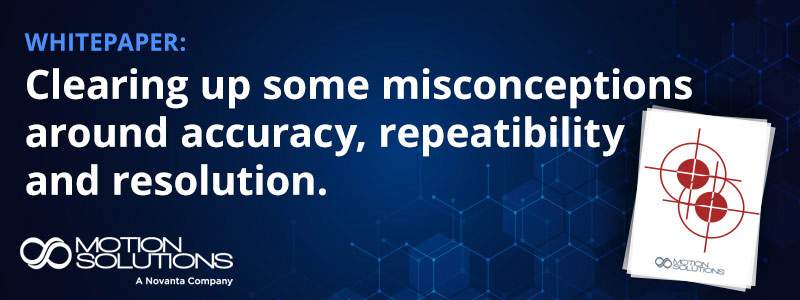
Clearing Up Some of the Misconceptions Around Accuracy, Repeatability, and Resolution
Introduction
Garbage in, garbage out doesn’t just hold for computer programming. Building a motion system that will effectively serve the application starts with properly defining performance requirements like accuracy, repeatability, and resolution. Unfortunately, a fair amount of confusion exists around these metrics (and other non-metrics) used to characterize positioning capabilities. Let’s take a closer look.
Positioning Metrics
We characterize the performance of a motion system by quantifying how effectively the actual motion corresponds to the commanded motion. For purposes of this discussion, let’s consider a simple motion system consisting of a screw-type stage advanced by a rotary servo motor. A controller sends commands to the drive, which powers the motor for a specific number of shaft rotations corresponding to the required displacement and acceleration; an encoder provides feedback for closed-loop operation.
Characterizing stage performance involves determining how effectively the stage maps input to output:
Input:
• Software input – a command from the controller to the drive
• Hardware input – the rotation of the motor shaft to turn the lead screw and advance the carriage
Output:
• Software output – the position reported by the encoder to the drive
• Hardware output – the real physical position of the carriage (typically measured by an external source such an interferometer)
There are two key metrics for quantifying the ability of a positioning stage to move to the commanded position: accuracy and repeatability.
What is accuracy?
Accuracy is a measure of the difference between the commanded position of the load (the software input) and the real physical position of the load (the hardware output). It can be determined by exercising the stage and measuring the load position with a laser interferometer (or similar external measurement device). Stage accuracy is critical to many applications, but the metric involves a number of caveats.
- An accuracy number only holds for that specific set up in the metrology lab at the manufacturer. Once the stage is shipped and installed at the customer location, performance can be impacted by mounting errors, changes to the electronics, and even environmental conditions. A mounting procedure detailing specifications like flatness of the mounting surface should be followed to ensure compliance to published spec.
- The accuracy of a linear positioning stage changes over the length of travel. The accuracy number provided may represent worst-case departure or just measurements taken at the center of the stage. A technique known as stage-error mapping – measuring steady state error down the length of travel and creating a lookup table used to back out error in the control loop – can be useful for certain applications but has a number of pitfalls.
- Different manufacturers express stage accuracy in different ways. Accuracies calculated using statistical methods such as RMS or 3 Sigma can be misleading, presenting an apparent stage accuracy that is better than the actual performance. As Figure 1 shows, a stage can be measured to have very good RMS accuracy without any single measurement achieving that performance and without consistently positioning the load in the same spot. To guard against this problem, ISO 230-2:2006, a standard for determining accuracy and repeatability of CNC machine tool positioning, focuses on maximum errors versus mean values.
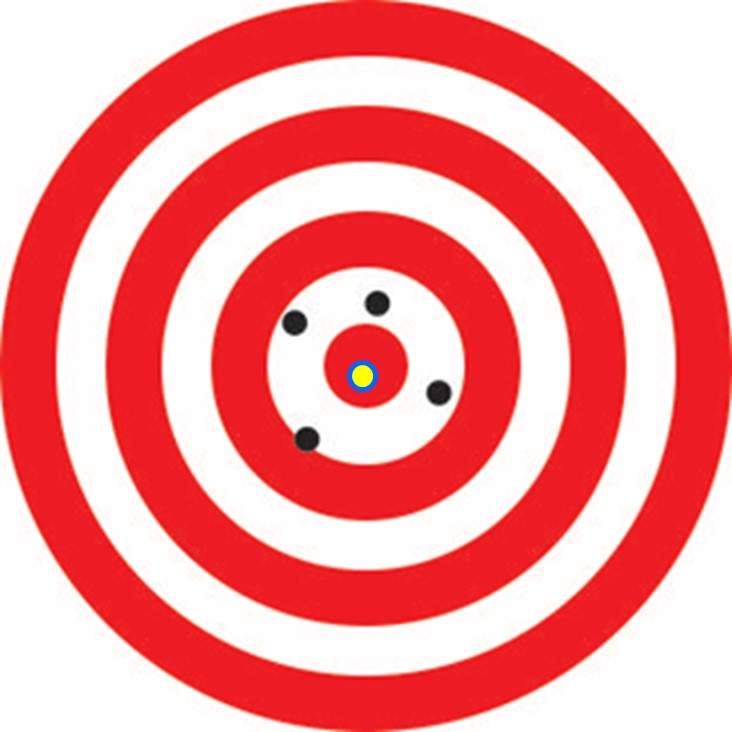
Figure 1: When accuracy is calculated as a mean, a stage can be characterized as highly accurate (yellow dot) without providing accurate or consistent positioning (black dots).
For demanding motion application, achieving high numerical accuracy is of limited use if the system can’t reliably position the load as needed. This brings us to the second essential motion system metric – repeatability.
What is repeatability?
Repeatability characterizes the consistency of motion system positioning. This metric quantifies how closely a stage can return to the same position when given the identical input command. There are two types of repeatability: unidirectional repeatability and bidirectional repeatability. For a given stage, unidirectional repeatability will be different than bidirectional repeatability.
Determining repeatability starts with commanding the stage to a specific position and measuring the error at a given position with a laser interferometer. This process is repeated across full range of motion. Two sets of data are collected, the first set in one direction and the second set in the opposite direction. Unidirectional repeatability is the deviation among all points in either data set, usually given as a +/- value for each. Bidirectional repeatability is the deviation among all points in the entire data set.
Factors influencing repeatability include torsional stiffness, friction, backlash, hysteresis, load, and acceleration/deceleration. In general, the unidirectional repeatability of a system will be better than its bidirectional repeatability.
As with accuracy, repeatability is a nuanced metric.
- Because unidirectional repeatability is typically better than bidirectional repeatability, it’s essential to know whether the repeatability numbers quoted for a stage are unidirectional or bidirectional. Determine whether the application is unidirectional or bidirectional before examining repeatability numbers and selecting a stage.
- Impressive repeatability alone isn’t necessarily enough. A stage can have high repeatability without being accurate (see figure 2). That said, if the system has poor accuracy but very high repeatability, it’s possible to leverage that consistency by correcting the error in software via a compensation table.
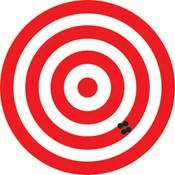
Figure 2: A stage can have high repeatability but low accuracy, making it ineffective for demanding motion applications.
3. Not all applications require high accuracy and high repeatability. In some cases, high repeatability is sufficient. The key is for the stage to perform with the repeatability and reliability required for the application.
What is resolution?
Now that we’ve talked about the two key performance metrics for stages, let’s turn to another common term that shows up in stage specifications – resolution. Resolution is probably the most widely misunderstood term used to describe stage performance. That’s because it’s used to characterize two distinct properties of a motion system: feedback resolution and mechanical positioning resolution.
Feedback Resolution
Feedback resolution is a property of the feedback sensor – in our case, an encoder –used in our closed-loop motion system. The resolution is the number of readings that the encoder can take per revolution (rotary encoder) or linear unit (linear encoder). In other words, resolution describes how granularly an encoder can monitor motor/stage motion. It does not tell us anything about the mechanical positioning capabilities of the stage itself.
Positioning Resolution
The metric that describes the fine-positioning capabilities of a stage is known as the minimum incremental motion. Minimum incremental motion is a combination of the baseline design plus any mechanical slop in the system. It is measured by exercising the stage in successively smaller increments while monitoring performance with a laser interferometer.
Now that we’ve defined our terms, let’s consider some of the subtleties.
- An encoder (or other feedback device) can only report stage motion. It cannot do anything to alter minimum incremental motion. If a motor can only reliably advance in 0.1° increments, adding an 18-bit encoder (0.0014° of rotation) won’t magically improve that. In fact, just the opposite may be true. If the drive or controller continually detects that the system is overshooting the commanded position because the minimum incremental motion is larger than the feedback resolution, the stage will simply hunt, increasing settling time and instability.
- Encoders don’t necessarily accurately measure the movement of the stage. In most motion systems, the encoder is mounted to track rotation of the motor shaft. The drive/controller uses that output to calculate changes to the position of the load. The problem is that this method is only as good as the mechanical performance of the stage. If there is a lot of slop in the system, the load may not advance as much as calculated by the feedback loop. For extremely demanding applications, it may be necessary to put an encoder on the load.
- Because a system cannot detect a change in motion without seeing a count, a stage can never be stable to better than +/-1 count.
- More isn’t necessarily better. OEMs sometimes specify ultrahigh resolution encoders to make their products more enticing. This can be an expensive and ineffective trap. Ultrahigh resolution feedback is really only useful for applications that need more counts in a small displacement, for example free space optical communication systems that need to hit a target a few feet across from hundreds of miles away, microscope focusing stages with depths of field only a few microns wide, and inspection systems locating molecule level imperfections in substrates.
- Resolution and minimum incremental motion don’t guarantee anything about overall stage performance. A stage can have very low minimum incremental motion and a high-resolution encoder without being either accurate or repeatable.
What about precision?
Precision is a descriptor often bandied about in discussions of motion systems and components. Although precision has a specific meaning in the measurement world, as defined by ISO 5725, that definition does not apply to motion control system performance.
Conclusion
Accuracy, repeatability, and minimum incremental motion are key characteristics that should be considered during the design and specification of a motion system. Remember, in the context of a motion system, these three quantities should be considered independent of one another. As summarized below, a stage can be presented as accurate (using statistical methods) without being repeatable, repeatable without being accurate, neither, or both (see Figure 3). Higher resolution isn’t necessarily better for a given application. The best stage to choose is the one that provides the combination of accuracy and repeatability that meet the particular needs of the application and the project, including budget.
Finally, and most importantly, understand how the manufacturer defines the performance metrics that appear on the datasheet. At Motion Solutions, we don’t apply statistical methods for metrics like accuracy. We base our procedures on ISO 230-2:2006, expressing accuracy and repeatability in terms of maximum error plus a safety factor, and share our raw data with customers upon request. Because clearly representing the actual performance of the stage benefits everyone.
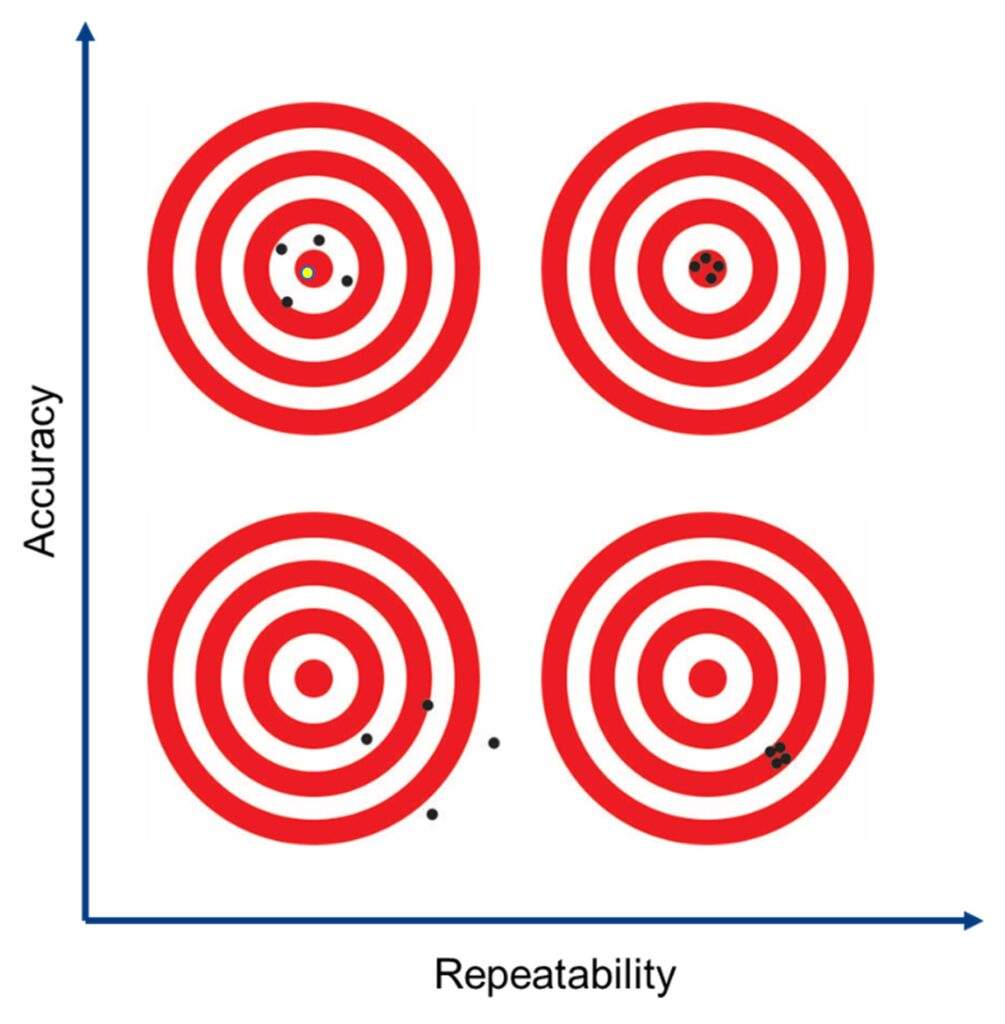
Figure 3: Graphics show (clockwise from top left) high accuracy (using statistical methods) but low repeatability, high accuracy and high repeatability, low accuracy but high repeatability, and low accuracy and low repeatability. Note that the yellow dot in the upper left-hand graphic is not the true accuracy but just the mean accuracy based on four in accurate readings.
Further Reading
Understanding the Benefits – and Limitations – of Stage Error Mapping
A Cost-Conscious Approach to Boosting Accuracy in Screw-Driven Stages
The engineering team at Motion Solutions has decades of aggregate experience in helping customers specify and build the ideal motion systems for their applications. To find out that we can help in your next project, contact us The engineering team at Motion Solutions has decades of aggregate experience in helping customers specify and build the ideal motion systems for their applications. To find out that we can help in your next project, contact Matt Luxton, Product Specialist.
About the Author
Matt Luxton | Product Specialist
Categories
- Case Studies
- Company News
- Customer Focus
- Engineering Insights
- Featured Products
- Industry Perspectives
- nPoint Blog
- Our Take
- Product Spotlight
- Uncategorized