A Piezo Stage can be characterized as a mechanical device, driven by a piezoelectric actuator, which provides one or more axis of motion. The term nanopositioning is used to indicate the technology of moving and measuring with nm precision. Piezo stages are used in nanopositioning applications since they can achieve that level of precision. nPoint designs and manufactures systems that use flexure hinges to link a moving platform to a static base. When used with closed-loop feedback, nPoint technology can provide excellent speed and linearity with nanometer resolution and accuracy.
A piezo stage can also be referred to as a nanopositioner, nanopositioning stage, piezo flexure stage, piezoelectric stage, or a nanopositioning device.
Here are the basic components of a flexure stage:
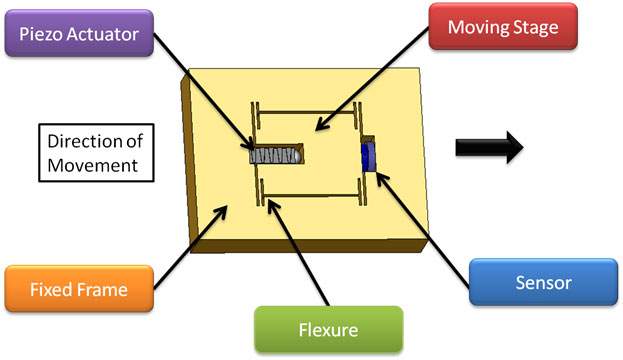
Benefits of Piezo Flexure Stages
- Great Reliability
- High-Speed Motion
- Billions of Cycles
- Millisecond Step and Settle Times
- Smooth Linear Motion
- Nanometer Positional Accuracy
- No Friction
- Operate in UHV Environments
- Extremely low Parasitic Motion
- Low Out-of-Plane Motion
- Long Term Stability
- Can Be Non-Magnetic
Possible Drawbacks
- Speed is Limited by Mechanical Resonance
- Travel is Limited to a Few Millimeters
- Power Must Be On to Maintain Position
A piezo stage is one portion of a closed-loop nanopositioning system which includes the following three items:
1. Nanopositioner
A flexure-guided piezo stage with a feedback sensor.
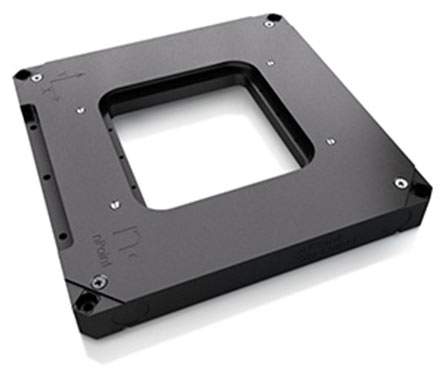
2. Nanopositioning Electronics
A controller necessary to provide closed-loop operation while providing positioning signals to the stage.
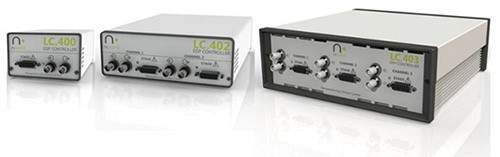
3. Nanopositioning Software
The software provides the means to interface with the controller and command the stage.
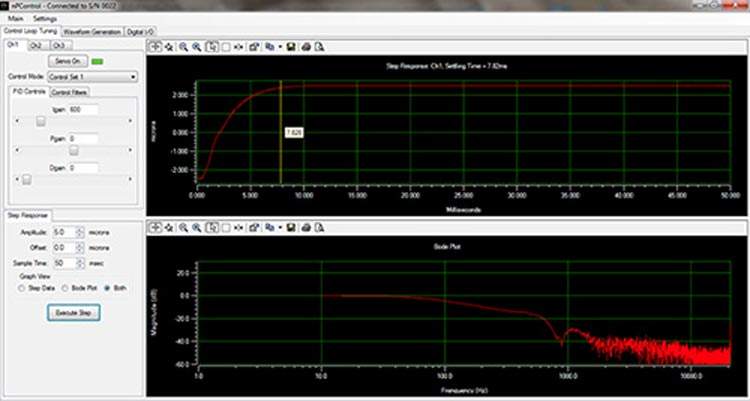
Software can be programmed to produce motion patterns appropriate to the desired application. Many different options are available to communicate with the controller. These can range from analog signals (-10V to 10V, 0 to 10V, etc.) to high-speed digital interfaces. The controller ensures the stage is in the desired position while providing the proper voltages to drive the piezo.
As part of a closed-loop system a piezo stage can precisely move an object to a relative position with respect to the fixed portion of the stage. To achieve the required motion precision, a controller is necessary to eliminate the nonlinearity, creep, and hysteresis issues that are inherent to the piezo itself.
Piezo stages come in many different dimensions and can provide travel ranges of up to 2mm, making them suitable for precision applications where longer travel ranges are not important. A piezo crystal can move about 0.1% of its length when voltage is applied. By providing a certain voltage to a piezo actuator it is possible to move a stage to a desired position. The piezo is designed to work within the flexure system and its motion can be amplified with the appropriate design. This provides larger range of motion in a smaller footprint. Finite Element Analysis (FEA) is used during the design of a flexure stage in an effort to optimize it for the customer’s application.
Nanopositioners come in many shapes and sizes used in a variety of applications. Each stage is designed with a specific application in mind but is often suitable for a variety of uses.