Optimize your precision motion system by following these 7 Tips for Selecting a Linear Bearing.
It’s easy to focus on motors and controllers when designing a motion system. When it comes to linear motion, however, bearing choice can make all the difference between a system that meets requirements and lasts and a system that doesn’t perform and fails prematurely. Here are 7 tips for Selecting a Linear Bearing to help you ensure that your linear motion system will serve the system and lead to happy customers.
1. Determine your requirements and priorities
All engineering involves trade-offs. Before starting to specify your linear bearing, understand the requirements of the system, including accuracy, size, smoothness of travel, lifetime, duty cycle, and cost. Develop an error budget for the system and determine the allowable contributions from the bearing. Be sure to prioritize all metrics so you can make effective decisions.
2. Understand error sources
A basic linear bearing system consists of a carriage riding on one or more rails. Precision motion systems typically use rolling elements such as balls or rollers to reduce friction. The two primary error sources in a linear bearing are:
- Running parallelism: Bearings have some deviation from absolute straightness as a result of machining and assembly tolerances, and mounting errors.
- Deflection: Excess clearance in the bearing can cause the load to deflect from intended position.
To improve running parallelism, machine mounting surfaces to tolerance and include alignment features. This can slightly increase cost but is generally well worth it. To decrease deflection, increase the preload; the trade-off is increased running friction, which can decrease motion smoothness and potentially reduce lifetime.
3. Don’t overlook the effects of orientation
Selecting a linear bearing starts with the layout, including the number of axes of motion, packaging constraints, etc. In combination with the load and the performance requirements, the layout drives the choice of rail and, ultimately, bearing. Be sure to take into consideration the effect of orientation. A Cartesian system hanging on the wall will be exposed to significantly different forces than one laid flat (see figure 1).
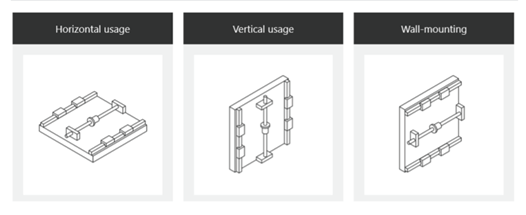
4. Include all loads
Proper sizing of the bearing is essential to achieving lifetime specifications. Loads can be classed as static or dynamic.
Static requirements
Determine the number of axes in the system and evaluate the loads for each axis (see figure 2). Start with the load type:
- Axial (thrust load): The load applies a force in the direction of travel.
- Radial load: The load applies a force orthogonal to the direction of travel.
- Moment load: The load applies a force at a distance, or torque around the axis. The moment direction may be described as Ma (pitch), Mb (yaw), Mc (roll).
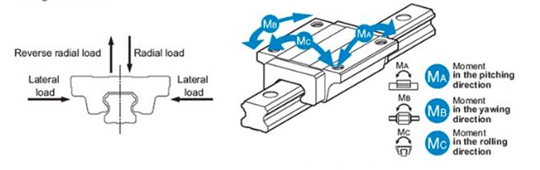
Calculate the force vectors (magnitude and direction) on an axis-by-axis basis and also for the assembly as a whole. Don’t forget to take into account both the applied load and any force introduced by the components of the machine itself. A patient bed, for example, might involve two or three stacked axes, so that the load on the lower axis includes not only the patient but the weight of the components that form the axes above. Start at the applied load and work through the stack.
Dynamic requirements
Dynamic loads include the static load of the mass, plus dynamic loads due to acceleration. In some cases, the machine itself may apply a load. Loads interact with one another. This particularly holds for complex motion stages, for which the dynamic forces change rapidly as various components reposition.
Again, start at the top layer and work your way through the stack. Try to keep the top layer as light as possible because the forces will be summed. This information will help determine the best choice of bearing.
5. Consider a dual-rail configuration
A single-rail might work well for a small, light load, even when it has an applied moment load. Heavier loads, particularly heavy moment loads, typically call for dual-rail systems (see figure 3). Widening the distance between rails reduces the reaction forces on the bearings, enabling them to better handle the applied moment.
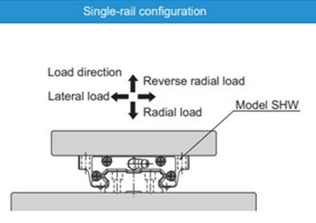
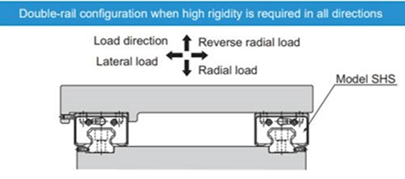
If the load is centered on the carriage, there is a greater possibility that a single-axis system will be enough. Wide square-rail designs increase the distance between the raceways, once again lowering the reaction forces and increasing the moment load that the single-rail bearing can support compared to conventional square-rail bearings. Perform a detailed mechanical analysis to gain the best understanding of system requirements.
6. Use caged bearings
Ball-type linear bearings can be specified with a ball cage, or separator. Molded to closely fit the surface of the balls, ball cages help ensure orderly movement for better high-speed performance. They minimize metal-to-metal contact, reducing wear and noise. The cages also do a better job of retaining grease, which increases bearing lifetime and maintenance intervals (see figure 4).
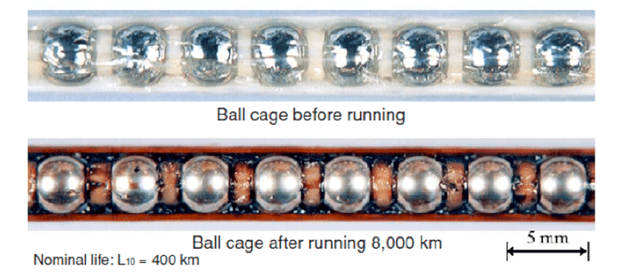
7. Design for duty cycle
How many cycles will the motion system run through over device lifetime? Thousands? Millions? Will there be a preventive maintenance program? Lower duty cycles may allow the use of low-cost, non-caged, single-row ball-type bearings bearing or even ball bushings. Higher duty cycles should use caged-ball-type bearings and may require the addition of a self-lubricator. Don’t forget that higher preloads can affect lifetime by increasing friction.
Conclusion
Selecting a linear bearing for your application begins with defining the requirements of the application upfront. Analyze that information in the context of the trade-offs discussed above to choose two or three of the most promising configurations for further exploration. Consider all details such as preload, cleanliness, seals, material requirements, lubrication, duty cycle, etc. Determine your priorities and then begin making trade-offs. Don’t forget that for sufficient volumes, customization is always a possibility.
For More Information
Learn more about how Motion Solutions can collaborate with you on your next at