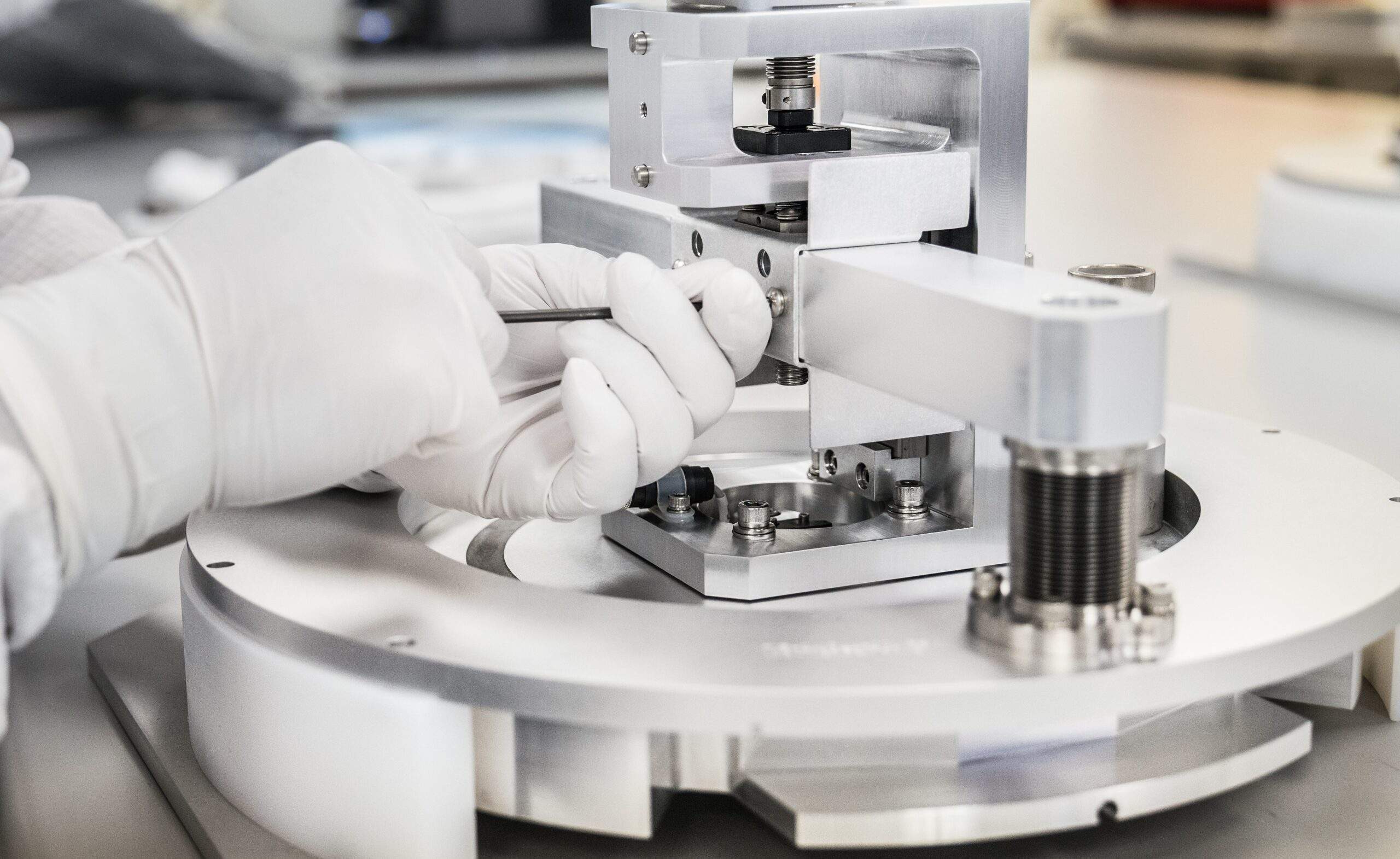
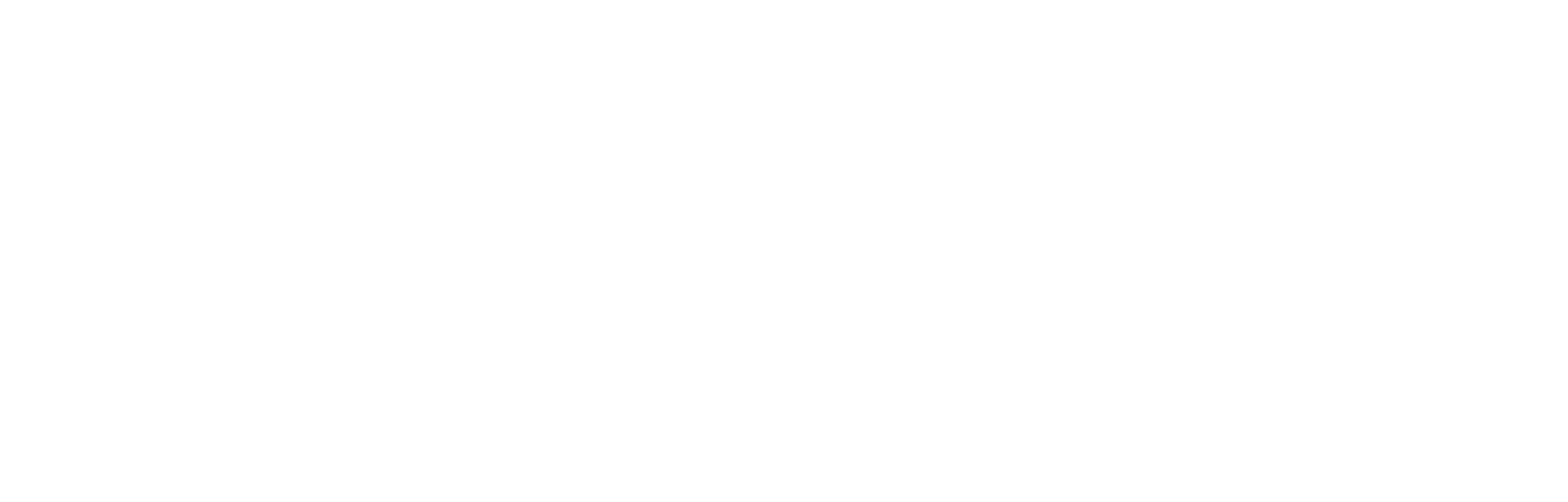
Portfolio
Motion Solutions provides custom, application-specific engineered solutions for motion control to OEM and industrial customers in the medical, life sciences, semiconductor, and industrial automation sectors. We offer a complete selection of engineering services, including electro-mechanical design, prototyping, and volume manufacturing. We’ve engineered thousands of solutions for motion control subsystems annually. Some are simple but we truly shine at designing and manufacturing highly complex, custom electromechanical subsystems. To get a better idea of the type of work we do, take a look at the sample projects below that demonstrate some of the engineered solutions for motion control we’ve created over the years.
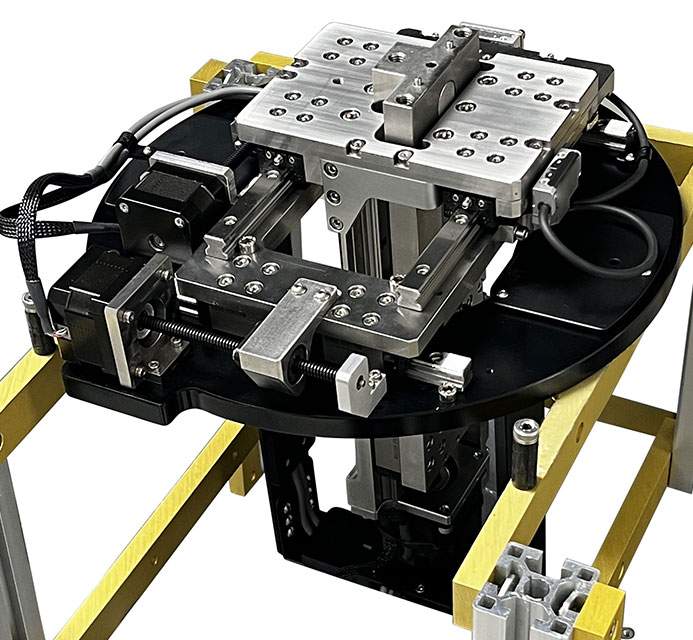
XYZ Stage for a high radiation, high-temperature environment
There were no matching results for your chosen filters.